Waldorf News
The Heart Bell: Community Building Through Artistic Creation
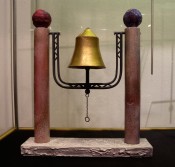
Schools are sometimes lucky enough to experience an artistic impulse that can serve as the foundation for community building. Bringing such a project to fruition is one of the most gratifying experiences a group can have. In tradition with the casting of bells at Ruskin Mill and Glasshouse Colleges, Freeman College was guided by Frank Chester and his ground-breaking discoveries in the casting of their bell on June 11, 2010. An artist, sculptor and geometrician from San Francisco, Frank explains his work and connection with Ruskin Mill Educational Trust in this interview with Ralph Sixsmith, a teacher at Freeman College.
What is a Chestrahedron?
A Chestahedron is a seven-sided form, also known as a septahedron, resting between a hexahedron and octahedron. “Septa” means seven and “hedron” means faces. Its significance is that the Chestahedron has not be found before although there is evidence that ancient schools as far back as 2000 years ago were studying such forms. The seven-sided form was found artistically. It took three months of failures using scientific approaches before I returned to my artistic training for a solution. I realized then that the points of the form were not equidistant from the centre, whereas normally they are in Platonic forms such as a hexahedron. I then took a ball of clay and went through a process of carving seven cavities, removing exactly the same amount of clay from each hole until the curvature of the ball disappeared. It effectively had straight lines, and 42 triangles. The cavities were filled with plaster of Paris and when, extracted and glued together, formed a crude Chestahedron.
How did you discover the Chestahedron had a relationship to the bell form?
I have developed my artistic process based on alchemy, which combines the elements of earth, air, fire and water. The Chestahedron was found using the element of earth followed by a water process. The only way I could do this was to make the Chestahedron flow. When I turned or spun the Chestahedron, the form turned into a bell. This was a complete surprise as I was not looking for this at all. If you watch the Chestahedron being spun, you will see a bell form, which reveals the secret geometry of the bell. Until then, bells had been designed by trial and error.
How did you come to be involved with Ruskin Mill Educational Trust and Freeman College?
A lady who knows my work, Patricia Dickson, brought Aonghus Gordon (Founder and Director of the Trust) to my home in California and within an hour or so of his arrival, Aonghus bought two of my sculptures and asked about a bell for Freeman College. Aonghus was clearly inspired! My part of this project was to ensure they followed the geometry properly. Secondly I wanted to make sure the bell isn’t mounted from the top. There isn’t a bell in history that hasn’t been hung by its neck! I wanted the whole bell to vibrate and not have any dead spots, which you can’t avoid if it is hung by the traditional method. So I designed a swinging ‘U’ shaped structure with a rod in the middle going up into the inside of the bell suspending it. This eliminates any dead portion and enables the bell to be supported by a clapper. Casting this bell and its design is truly a world event because this is the first time a lawful geometric etheric form has been cast.
What connection does a Chestahedron have to the human heart?
Finding this new lawful geometric etheric form meant that a new process based on expanding a Platonic form rather than the usual reductive approach of compressing or truncating can now be used. In my approach and understanding, this seven-sided form lies between warmth and light, which is the area of the human heart. When this form was spun on the end of a high-speed drill at an angle of approximately 36 degrees, a type of pocketshaped vortex developed. I sculpted a model of this vortex and in cross-section; it resembled the cross section of a human heart. I found the Chestahedron is balancing between accelerating and decelerating vortexes. This form is a brake. I concluded that the heart’s basic form and function is not to pump blood but to regulate blood flow. For example, the faster the heart beats the less the blood flows, therefore it is not a pump but a regulator. Also the apex of the heart is paper-thin and would blow out if the heart were just a pump. This discovery means that we can talk about the heart objectively as it is following lawful geometry.
What is the significance of casting the bell in Sheffield?
This bell has been around in my workspace for ten years and Aonghus was the first person to pick it up. I kept asking myself: Why England and why Sheffield? When I visited the Millennium Galleries in Sheffield, I understood why, because of the craftsmanship and heritage of working with metal that has been going on for 700 years or so. The Liberty bell, to celebrate independence in the USA, was cast here in England in1752 and so this country has a long history of making bells. I went to many bell casters in California to get one of these bells made for myself but no one would combine 15% of tin with 85% of copper. Why? Well, since the Second World War, they quit using tin, replacing it with silicon and never returned to using tin again.
And what of the future?
I have envisioned using my techniques of stirring and moving water with Chestahedron variations to develop new ideas in Biodynamic preparations and embryology studies. I would like to thank the whole team of teachers, craftsmen, staff, students and helpers at Freeman College who worked so hard in making the Heart Bell possible. It was a joy to work with you all.
Casting the Heart Bell
The bell casting team was headed by Bill Benton who has cast the previous bells at our colleges. Bill was assisted by Carole Baugh, Duncan Ince, Danny Rowan, Ralph Sixsmith and student Thomas Stockton, as well as hands-on support from many staff and students at Freeman College. The team also included Tony Ind and Paul Gittins from Glasshouse College.
The furnace is powered by natural gas from the gas main and electricity from a studio. There will be approximately 160 kgs of copper, 40 kgs of tin, 5 kgs of phosphor copper and a small amount of gold. These materials will be in the furnace for as long as necessary and melted. We hope this will be enough to cast the bell but we have spare copper and tin if necessary. The furnace was brought up from Glasshouse College following their bell casting six years ago. The six casting boxes have been borrowed from Brass Founders in Sheffield and are one of our sponsors. We have been working on this project since Easter and initially went down to Stourbridge to look at the furnace, then transport it up here.
We have refurbished it with some of our students which included taking the burner out and sorting the bricks out. The major problem has been the weather as it is in the courtyard. We got the moulding sand from Brass Founders and added Bentonite or dry clay which holds the shape of the cast when it dries. The drawings had to be made to scale and conform to Frank Chester’s geometric plan according to the Chestahedron. This shape has never been cast before, as far as we know. We had to get straw to make straw rope for the centre of the bell mould and this was made by the students in Sterling Works courtyard. All the boxes for the bell mould were filled with sieved sand around the drag (centre) of the bell to form the mould proper. When dry, these were lifted off to reveal the exterior of the bell. We then removed the clay from the centre of the bell and cleaned up the inside of the mould to get the best finish possible. We put the moulding boxes back over the model, bolted them together and fitted a slag pot into which we will pour the molten metal.
Once cooled the Heart bell was revealed for the staff and students of Freeman College to see. The next stage for this 2.5 cwt bronze bell is turning and tuning. We will not know the note that this bell makes until it is can hang freely, allowing its natural voice to be heard.
Ralph Sixsmith, tutor
The interview and accompanying article originally appeared in the Summer 2010 issue of Run of the Mill: The Ruskin Mill Educational Trust Magazine. The article, with many photos of the entire process, can be viewed at Frank Chester’s web site.